Waterside Security Barrier Design Considerations
Designing Your Barrier
Protecting your waterborne assets starts with an expertly designed barrier system made to meet your exact needs.
Designing a waterside security barrier system is a complex engineering task that is a careful balance of requirements, available technology, budget, schedule, and life cycle cost expectations. Each of these constraints must be evaluated considering the needs for each unique project. For simple warning type barriers, a simple off the shelf solution is often the answer. For waterside security protection of high value warships, nuclear power plants, refineries, and other important land assets with a waterside vulnerability, there must be an engineered solution.
At HALO, we focus on giving access control where essential, such as with warship or cruise ship protection. For all our projects, safety of personnel and security of the protected assets control the design process.
A floating barrier that merely provides water level protection is insufficient; newer solutions such as the HALO™ system provide a barrier that extends eight feet above water level, making it impassable to small craft users. This transition from first generation boom systems towards integrated fortifications allows for a complete denial of physical entry above and below the water level. These barriers are highly engineered solutions to unique installation security.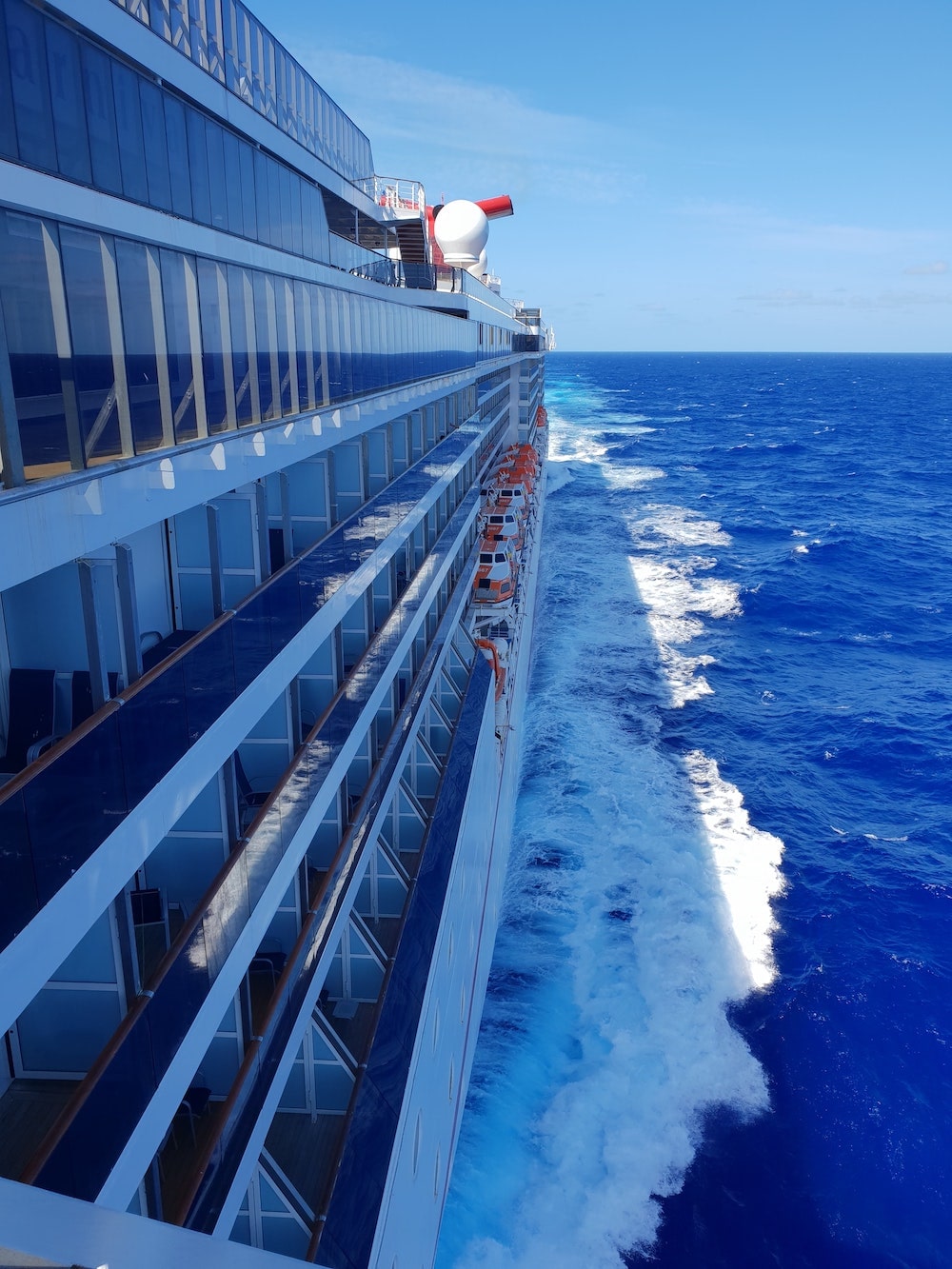
Requirements for each project may come from a wide variety of sources
- For U.S. Navy projects, there are OPNAV Instructions, MilSpecs, and a wide range of security directives that must be consulted
- The nature of the high value asset and its inherent waterside vulnerability must be studied to provide adequate control, warning, and threat zones with standoff from public areas
- Some intelligence assessment must be made to base the threat on “credible” assumptions for the type, size, speed, and many other capabilities of the threat. Not every threat can be protected against when each project is under budget constraints
- Underwater threats require special engineering work for underwater nets, diver detection sensor, or other more sophisticated systems
- Land side security systems must be considered as well to make sure the whole security system for the asset is consistent
- Testing requirements can be critical. Not all systems have been tested in any operational environment by credible testing agencies. Real world operational testing should always be a consideration
- Environmental issues with waterside areas have to be considered
- Budget and schedule always have to be considerations in the final design
- Life cycle costs should be a strong input into the design. Maintenance costs can quickly overtake purchase costs for a system if it requires frequent out of the water inspections and repairs. Proper choice of barrier materials and solid engineering can greatly reduce life cycle costs for these security barrier systems.
Maintenance considerations might include areas like:
- How often does the system need to be hauled out, inspected, sand blasted, and repainted (if metal)
- Is the barrier temporary or permanent? What’s the expected operational life of the barrier system
- What’s the corrosion resistance of all the component parts
- Are there dissimilar metals used that will cause rapid galvanic corrosion
- Repair philosophy: can minor repairs be performed with the system in operation
- Reliability of access gates, deployable nets, or other moving parts
- Reliability of mooring systems and the barrier in storm conditions. Storm damage resistance should be a large input into the design because of the safety considerations and the cost of repairs from storms can be very high
Not sure what barrier is best for you?
Six Questions To Get the Right Barrier For Your Project
Barrier Selector ToolAccess requirements will be a major design input. A key input to the design is whether a gate is needed and if so, does it need to be automatic.
- For ship or other moving assets to be protected, easy access into and out of the barrier system is essential. This must be quick, safe, and reliable. The barrier should have very little operational impact on the assets protected
- Automated access gates are available from HALO for any of the barrier system we design. Automation provides significant increases in safety of personnel and is usually a quicker way to provide the needed access
- Manual gates which require personnel to manipulate gates from small boats should generally be resisted. These systems are usually safety hazards in higher sea conditions
- Sea condition limits for the gate operation must be considered. This is a balance of local conditions at the site, and the operational needs of the asset. For example, an Aircraft Carrier may need to get underway for storm evasion after the seas are high in advance of the storm. The access gate has to work.
Systems Integration requirements will vary with each project. For some sophisticated projects there may be integration with a shore side C4I system using an array of sensors, monitoring systems, manned command systems, and even weapons systems. These all require detailed engineering to add sensors to the barrier system, provide system feedback into the overall security monitoring system. Inputs like Gate open/shut become important parts of the overall security posture.
Materials Selection has a huge impact on life cycle cost of waterside security barriers and can also impact reliability to a large degree. HALO barrier systems utilize the most modern materials that are both low maintenance and environmentally friendly. Employing advanced composite materials, the HALO barriers can work with nature, not fight it. This means significantly less maintenance in the harshest marine environments.
Mooring Engineering is a significant HALO strength. Mooring a long barrier system so it can withstand both the forces of nature AND the impact of swarms of fast boat threats can be a real challenge. The mechanical and ocean engineering team at HALO has the expertise to design each mooring system based on all the inputs from the range of weather expected at the site, to the bottom type, to the length, displacement, drag and more parameters of the barrier itself. Installing a great barrier that isn’t moored properly, with sound engineering, is no solution at all.